Manufacturing Leadership Master of Science Degree
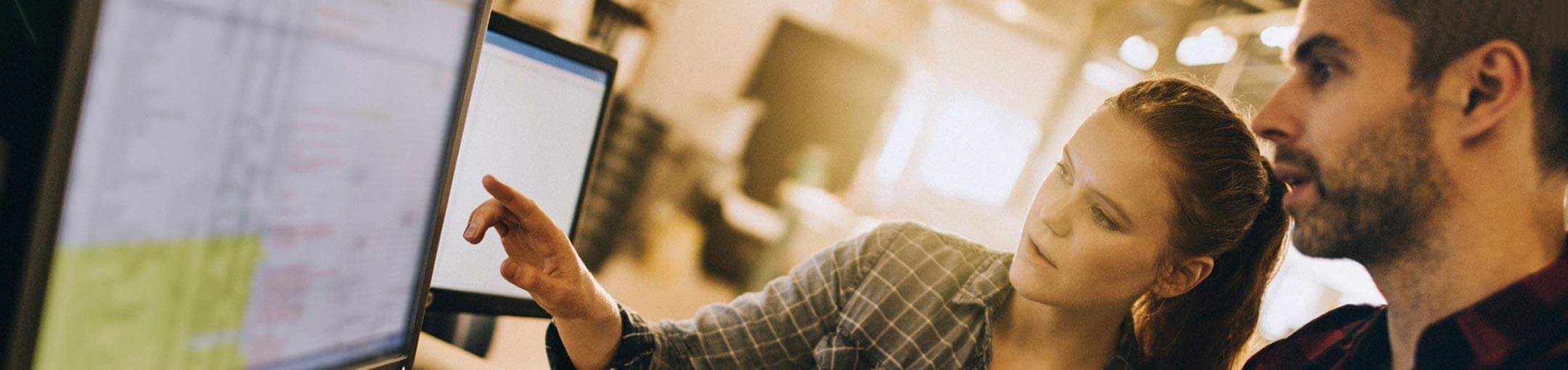

Manufacturing Leadership
Master of Science Degree
- RIT /
- College of Engineering /
- Academics /
- Manufacturing Leadership MS
Department of Engineering Leadership
Providing experienced engineers and business professionals with the leadership skills to optimize business operations in a range of organizations and industries.
Overview for Manufacturing Leadership MS
Why Study Manufacturing Leadership at RIT?
- Career Readiness: Gain the skills necessary to secure a high-level position in operations, supply chain management, or process improvement.
- Flexibility: Starting any term you choose, complete online or on-campus courses at your own pace.
- Exciting Capstone Project: Receive the opportunity to solve a real-world problem for a sponsoring employer in operations or service management.
The manufacturing leadership master's is for experienced engineers and other professionals who aspire to high-level positions in operations, supply chain management, and process improvement. The degree in manufacturing management integrates business and engineering management courses, delivering them online or on-campus, where you may continue to work while taking classes.
The master's in manufacturing engineering leadership is a focused program developed jointly by the Kate Gleason College of Engineering and Saunders College of Business. Particular emphasis is placed on supply chain management, global manufacturing and operations, lean systems thinking, leadership, and decision-making.
A capstone project, oriented to solving an operations or service management problem or process improvement initiative, enables you to apply new skills and capabilities to solve a pressing real-world problem with significant financial benefit to your sponsor.
The manufacturing leadership master's can also be taken on a full-time basis, with several courses available on campus. You may start any term (fall, spring, summer) and complete courses at your own pace.
Capstone Project Sponsorship
For the capstone project, you will be sponsored by an employer who is committed to improving leadership capabilities in operational excellence. Sponsorship includes financial support and a commitment to work with you to provide clear expectations and a well-articulated career development plan that builds upon the program. As an alternative, you are welcome to sponsor yourself. You may contact Financial Aid and Scholarship for more information.
Related Programs
Visit the Engineering Leadership department for information on related offerings, including the master of science in product development, graduate certificate programs, and non-credit workshops and training programs.
Programs are available online, on-campus, or onsite at your location. Contact us for information about partnerships and customized programs for your organization.
Join us for Fall 2024
Many programs accept applications on a rolling, space-available basis.
Featured Profiles
Dag Lindquist
Corning Advanced Optics - Manager, Manufacturing and Service
“After many years in manufacturing, stepping back into the classroom offered a refreshing recharge for my career. Top notch faculty with industry experience, along with the diverse industry experience...
Linda Marks
Corning Incorporated - Manager of Characterization Sciences Global Lab Support
“My capstone project provided immediate and long-term savings to Corning that more than covered the cost of attending the program. The diversity of thought and broad experiences of faculty and...
Matthew Crump
BorgWarner Morse Systems - Senior Engineer
“The skills and toolsets learned through the MML program provided me the opportunity to lead a global cross-functional team in pursuit of the first business partnership between Morse Systems Ithaca...
Curriculum for 2023-2024 for Manufacturing Leadership MS
Current Students: See Curriculum Requirements
Educational Objective
To prepare graduates to lead teams and organizations within a manufacturing or service enterprise for successful competition in a complex global economy, through the integration of business and technical skills.
Key Capabilities of Graduates
- Ability to make sound business decisions in a complex global economy: business planning with full understanding of outsourcing and offshoring; financial management and total/life-cycle cost; agile decision-making.
- Ability to manage the global supply chain: supply chain strategy development and execution; logistics management (quality and delivery assurance); systems needs for supply chain management; and supply chain optimization.
- Ability to manage global, multi-site production and operations: managing distributed teams; process technology transfer to domestic and international locations; service operations; enterprise and manufacturing strategies; lean operations; location strategy and facility design; state-of-the-art tools; regulatory issues and established norms.
- Comprehensive understanding of quality and continuous improvement principles, with application to the manufacturing and operations management.
- Strong leadership and management skills applied to global high technology manufacturing: systems thinking, planning, and management; applications (“hands-on”) orientation; project management expertise (planning, relationship management, control, risk management and decision-making); creative leadership to drive innovative solutions; enhanced ability to recognize barriers to success early, when corrective actions are least costly.
Manufacturing Leadership, MS degree
Course | Sem. Cr. Hrs. | |
---|---|---|
ISEE-682 | Lean Six Sigma Fundamentals This course presents the philosophy and methods that enable participants to develop quality strategies and drive process improvements. The fundamental elements of Lean Six Sigma are covered along with many problem solving and statistical tools that are valuable in driving process improvements in a broad range of business environments and industries. Successful completion of this course is accompanied by “yellow belt” certification and provides a solid foundation for those who also wish to pursue a “green belt.” (Green belt certification requires completion of an approved project which is beyond the scope of this course). (This course is restricted to degree-seeking graduate students and dual degree BS/MS or BS/ME students in KGCOE.) Lecture 3 (Fall, Spring, Summer). |
3 |
ISEE-703 | Supply Chain Management Supply chain management is unique in that it is one of the oldest business activities and yet has been recently discovered as a potentially powerful source of competitive advantage. Supply chain system activities, such as planning production levels, forecasting demand, managing inventory, warehousing, transportation, and locating facilities have been performed since the start of commercial activity. It is difficult to visualize any product that could reach a customer without a consciously designed supply chain. Yet it is only recently that many firms have started focusing on supply chain management. There is a realization that no company can do any better than its supply chain and logistics systems. This becomes even more important given that product life cycles are shrinking and competition is intense. Logistics and supply chain management today represents a great challenge as well as a tremendous opportunity for most firms. (This course is restricted to degree-seeking graduate students or ISE department dual degree students.) Lecture 3 (Spring). |
3 |
ISEE-723 | Global Facilities Planning Facilities planning determines how an activity's tangible fixed assets best support achieving the activity's objective. This course will provide knowledge of the principles and practices of facility layout, material handling, storage and warehousing, and facility location for manufacturing and support facilities. Tools for sizing the resources needed, planning, design, evaluation, selection, and implementation will be covered. The focus of the course will cover both management and design aspects, with the focus being more heavily on the management aspects. (This course is available to RIT degree-seeking graduate students.) Lecture 3 (Fall). |
3 |
ISEE-745 | Manufacturing Systems This course will provide an introduction to concepts and techniques in the design and analysis of production systems. A blend of traditional and modern approaches is brought into the classroom. At the end of the term, the student will be able to assess and analyze the performance of a given manufacturing system as well as to provide a framework for system redesign and improvement. Modern aspects such as lean manufacturing and setup time reduction are included in the context of the course. (This class is restricted to degree-seeking graduate students or those with permission from instructor.) Lecture 3 (Spring). |
3 |
ISEE-771 | Engineering of Systems I The engineering of a system is focused on the identification of value and the value chain, requirements management and engineering, understanding the limitations of current systems, the development of the overall concept, and continually improving the robustness of the defined solution. EOS I & II is a 2-semester course sequence focused on the creation of systems that generate value for both the customer and the enterprise. Through systematic analysis and synthesis methods, novel solutions to problems are proposed and selected. This first course in the sequence focuses on the definition of the system requirements by systematic analysis of the existing problems, issues and solutions, to create an improved vision for a new system. Based on this new vision, new high-level solutions will be identified and selected for (hypothetical) further development. The focus is to learn systems engineering through a focus on an actual artifact (This course is restricted to students in the ISEE BS/MS, ISEE BS/ME, ISEE-MS, SUSTAIN-MS, PRODDEV-MS, MFLEAD-MS, ENGMGT-ME, or MIE-PHD programs or those with 5th year standing in ISEE-BS or ISEEDU-BS.) Lecture 3 (Fall, Spring). |
3 |
MGMT-740 | Leading Teams in Organizations This course examines why people behave as they do in organizations and what managers can do to improve organizational performance by influencing people's behavior. Students will learn a number of frameworks for diagnosing and dealing with managerial challenges dynamics at the individual, group and organizational level. Topics include leadership, motivation, team building, conflict, organizational change, cultures, decision making, and ethical leadership. Lecture 3 (Fall, Spring, Summer). |
3 |
Choose one of the following: | 3 |
|
PROF-710 | Project Management This course addresses project management from a multidisciplinary perspective, covering the fundamental nature of and techniques for managing a broad range of projects. Topics cover the Project Management Life Cycle from Planning to Termination. It also addresses the behavioral and quantitative facets of project management, as well as the use of methods, tools and techniques for the initiation, planning, and execution of projects. Introduces the standard framework, processes and knowledge areas of the Project Management Institute. *Note: Bachelors degree or minimum of 5 years of work experience in a project related business environment. Recommended education or work experience in organizational behavior, mathematics and basic accounting. *Note: BUSI-510 may not be substituted for BUSI-710 in a graduate concentration or the advanced certificate in project management. Additionally, a student may not register for and receive credit for both BUSI-510 and BUSI-710, whether taken as an undergraduate or graduate student. (This class is restricted to degree-seeking graduate students or those with permission from instructor.) Lecture 3 (Fall, Spring, Summer). |
|
PROF-714 | Agile Project Management Business agility allows organizations to quickly adapt to new markets. In a fast paced ever changing world of highly competitive products and services, organizations need to be able to deliver solutions to market quickly in an uncertain environment. Agile Project Management provides an iterative and incremental framework to explore and deliver high risk solutions efficiently in a rapid response timeframe. We will explore Agile Project Management practices across multiple industries including Agile project roles following the Project Management Institute® Agile Practice Guide. (This course is available to RIT degree-seeking graduate students.) Lecture 3 (Fall, Spring). |
|
ISEE-750 | Systems and Project Management This course ensures progress toward objectives, proper deployment and conservation of human and financial resources, and achievement of cost and schedule targets. The focus of the course is on the utilization of a diverse set of project management methods and tools. Topics include strategic project management, project and organization learning, chartering, adaptive project management methodologies, structuring of performance measures and metrics, technical teams and project management, risk management, and process control. Course delivery consists of lectures, speakers, case studies, and experience sharing, and reinforces collaborative project-based learning and continuous improvement. (Prerequisites: ISEE-350 or equivalent course or students in ISEE BS/MS, ISEE BS/ME, ISEE-MS, SUSTAIN-MS, ENGMGT-ME, PRODDEV-MS, MFLEAD-MS, or MIE-PHD programs.) Lecture 3 (Fall). |
|
Choose one of the following: | 3 |
|
ACCT-603 | Accounting for Decision Makers A graduate-level introduction to the use of accounting information by decision makers. The focus of the course is on two subject areas: (1) financial reporting concepts/issues and the use of general-purpose financial statements by internal and external decision makers and (2) the development and use of special-purpose financial information intended to assist managers in planning and controlling an organization's activities. Generally accepted accounting principles and issues related to International Financial Reporting Standards are considered while studying the first subject area and ethical issues impacting accounting are considered throughout. (This class is restricted to degree-seeking graduate students or those with permission from instructor.) Lecture 3 (Fall, Spring, Summer). |
|
ACCT-794 | Cost Management in Technical Organizations A first course in accounting for students in technical disciplines. Topics include the distinction between external and internal accounting, cost behavior, product costing, profitability analysis, performance evaluation, capital budgeting, and transfer pricing. Emphasis is on issues encountered in technology intensive manufacturing organizations. *Note: This course is not intended for Saunders College of Business students. (Enrollment in this course requires permission from the department offering the course.) Lecture 3 (Spring). |
|
Choose one of the following: | 3 |
|
ISEE-792 | Engineering Capstone Students must investigate a discipline-related topic in a field related to industrial and systems engineering, engineering management, sustainable engineering, product development, or manufacturing leadership. The general intent of the engineering capstone is to demonstrate the students' knowledge of the integrative aspects of a particular area. The capstone should draw upon skills and knowledge acquired in the program. (This course is restricted to students in ISEE-MS, ENGMGT-ME, SUSTAIN-MS, PRODDEV-MS, MFLEAD-MS or the ISEE BS/MS programs.) Lecture 3 (Fall, Spring). |
|
ISEE-793 | Manufacturing Leadership Capstone For the MS in Manufacturing Leadership program. The purpose of the project is for students to demonstrate integrative application of knowledge and skills acquired during the program. A capstone project will be oriented to the solution of a manufacturing, operations, or supply chain management problem or to a technically related process. A suitable project will be multi-disciplinary or multi-functional in nature and will have significant impact on one or more competitive capabilities of the organization, e.g., quality, lead time, cost, flexibility, or service. Team-based projects are encouraged. Projects must be approved in advance of registration. (This course is restricted to MFLEAD-MS Major students.) Lecture 3 (Fall, Spring). |
|
Engineering Elective or other non-Business Elective |
3 | |
Total Semester Credit Hours | 30 |
Elective courses
An elective course offers students the opportunity to better meet personal and organizational needs. Students may select from a long list of courses. Recommended electives include such offerings as Decision and Risk Benefit Analysis, Advanced or International Project Management, Breakthrough Thinking and Creativity, Customer Centricity, and others.
Capstone project
Students complete a project during the final academic year of the program, based on a real problem often identified in the companies where they work. The corporate-oriented capstone project is directed at the solution of a manufacturing or services management problem or process improvement initiative. It enables students to broaden the educational experience and demonstrate the knowledge and skills essential to business leadership. The project provides immediate benefits to sponsoring organizations and is an excellent opportunity for students to gain visibility and recognition. Projects often result in substantial cost savings or improved efficiencies. View our list of capstone projects for examples of projects past students have completed as part of the program.
Note for online students
The frequency of required and elective course offerings in the online program will vary, semester by semester, and will not always match the information presented here. Online students are advised to seek guidance from the listed program contact when developing their individual program course schedule.
Admissions and Financial Aid
This program is available on-campus or online.
On Campus
Offered | Admit Term(s) | Application Deadline | STEM Designated |
---|---|---|---|
Full-time | Fall or Spring | Rolling | Yes |
Part-time | Fall or Spring | Rolling | No |
Online
Offered | Admit Term(s) | Application Deadline | STEM Designated |
---|---|---|---|
Full-time | Fall or Spring | Rolling | No |
Part-time | Fall or Spring | Rolling | No |
Full-time study is 9+ semester credit hours. Part-time study is 1‑8 semester credit hours. International students requiring a visa to study at the RIT Rochester campus must study full‑time.
Application Details
To be considered for admission to the Manufacturing Leadership MS program, candidates must fulfill the following requirements:
- Complete an online graduate application.
- Submit copies of official transcript(s) (in English) of all previously completed undergraduate and graduate course work, including any transfer credit earned.
- Hold a baccalaureate degree (or US equivalent) from an accredited university or college.
- A recommended minimum cumulative GPA of 3.0 (or equivalent).
- Submit a current resume or curriculum vitae.
- Submit a personal statement of educational objectives.
- Submit one letter of recommendation.
- Entrance exam requirements: None
- Writing samples are optional.
- Submit English language test scores (TOEFL, IELTS, PTE Academic), if required. Details are below.
English Language Test Scores
International applicants whose native language is not English must submit one of the following official English language test scores. Some international applicants may be considered for an English test requirement waiver.
TOEFL | IELTS | PTE Academic |
---|---|---|
79 | 6.5 | 56 |
International students below the minimum requirement may be considered for conditional admission. Each program requires balanced sub-scores when determining an applicant’s need for additional English language courses.
How to Apply Start or Manage Your Application
Cost and Financial Aid
An RIT graduate degree is an investment with lifelong returns. Graduate tuition varies by degree, the number of credits taken per semester, and delivery method. View the general cost of attendance or estimate the cost of your graduate degree.
A combination of sources can help fund your graduate degree. Learn how to fund your degree
Additional Information
Prerequisites
Applicants must have at least two years of experience in a manufacturing-related organization or business environment.
Online Degree Information
The Manufacturing Leadership MS program is designed to be completed part-time (1 or 2 courses per term). Full-time options may be available with Graduate Program Director's approval. Time to completion will depend on the plan of study when courses are offered, selected electives, and if the student takes a summer course. Courses may be synchronous or asynchronous. Academic advisors work with students on a study plan after admission to ensure classes fit student availability. Typically students finish this degree in 24-36 months. For specific details about the delivery format and learning experience, contact the Program Contact listed on this page. RIT does not offer student visas for online study.
Online Tuition Eligibility
The online Manufacturing Leadership MS is considered a professional degree that is billed at the standard (on campus) RIT graduate tuition rate. It is not billed at the designated online tuition rate. Scholarship is available off the standard tuition rate for this online program. View the current Graduate tuition rate.
Online Study Restrictions for Some International Students
Certain countries are subject to comprehensive embargoes under US Export Controls, which prohibit virtually ALL exports, imports, and other transactions without a license or other US Government authorization. Learners from the Crimea region of the Ukraine, Cuba, Iran, North Korea, and Syria may not register for RIT online courses. Nor may individuals on the United States Treasury Department’s list of Specially Designated Nationals or the United States Commerce Department’s table of Deny Orders. By registering for RIT online courses, you represent and warrant that you are not located in, under the control of, or a national or resident of any such country or on any such list.